Reid Ozaki
1951 - 2024
Remembering Reid Ozaki
“...Ozaki has become one of the area's most respected potters.”
Matthew Kangas; Ceramics Monthly, November 2009
In the past I have made changes in my work, some were gradual, some abrupt, but always it seems, the changes have been linear. Recently, I have found myself in the unusual and somewhat uncomfortable position of having several different ideas competing for time and attention in my work. At the moment, I find myself torn between working on one new idea or the next and back. While I am finding each direction to be rewarding in itself, frustration comes from the lack of time to fully pursue a new idea to its ultimate conclusion. That can only come from making the pots and unfortunately with clay that takes time. It is an exciting time making pieces from ideas that have been relatively fully examined as well as work from ideas that will develop further.
Soda Firing:
Sodium Vapor firings have been a part of the potter's technology since the 13th century. Developed in Germany using salt as the source of the sodium it was eventually adopted throughout the ceramics industry. Studio potters found the typical "orange peel" texture of the glaze attractive and durable. In most Vapor firings, ware is placed in the kiln unglazed. The potter fires the kiln to the maturing temperature of the clay then introduces a source of sodium into the kiln. The heat of the firing causes the sodium compound to dissociate into sodium ions. The sodium in this form is carried through the ware by the draft of the kiln combining with silica along the way to create a sodium-silicate glaze on everything in the kiln including the ware. Soda firing was developed as a technique for firing ceramics in the 1970's. Developed as an environmentally friendly alternative to the traditional salt firing, soda ash and other sodium compounds were used in place of salt. The results were disappointing though. Unlike salt, other soda compounds do not travel well throughout the kiln and the effects were spotty. It was in the mid-1990s that potters began to see and appreciate the qualities of Soda firing in its own light instead of seeing only soda's inability to reproduce Salt firing glaze effects. Since then, much research has gone into taking full advantage of Soda firing's unique characteristics. Many variables are being tested including basic kiln design, the timing and method of introduction of the soda during the firing, and clay body composition. Other important variables include the form of the work, applied slips and glazes and how and where pieces are loaded into the kiln. Manipulation of the kiln atmosphere (the ratio of air to gas) is also important in the final outcome. With all these variables in play the potential for failure is high. But when everything comes together, Soda firing can produce beautiful and unique results.
Ikebana and Chanoyu:
From very early in my life, I have been surrounded by the traditional Japanese arts. My strongest influence was my grandfather’s love of Bonsai, gardens and plants. When I started my ceramic career, this very naturally led to an interest in the art of Ikebana, then to Chanoyu. The study of Tea and the making of the utensils are the key to the aesthetic I am trying to understand. I make tea utensils with the understanding that I have much to learn.
I am more comfortable making flower containers for Ikebana. There is more freedom to explore the potential of a new approach using new materials and glazes. In Ikebana, the container is not viewed as a separate entity, but rather as an integral part of the whole. It must not detract from or overwhelm that which it contains.
Tableware:
For many years, I have come up with numerous reasons to avoid making tableware. The annual series of Glenn Richards Mingei (folk pottery) Pottery Invitational exhibitions has inspired me get over this reluctance and get back to the roots of what we, as functional potters, do. I have gotten surprising pleasure from designing and making items for the table.
Wood firing:
I have joined John Benn and Colleen Gallagher in their venture in wood firing at their kiln on Harstine Island, WA. In all wood fired kilns, happy results are never guaranteed. When the pots do turn out, they are beautiful and unique.
1951 - 2024
Remembering Reid Ozaki
“...Ozaki has become one of the area's most respected potters.”
Matthew Kangas; Ceramics Monthly, November 2009
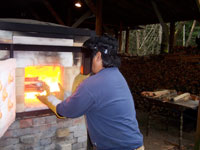
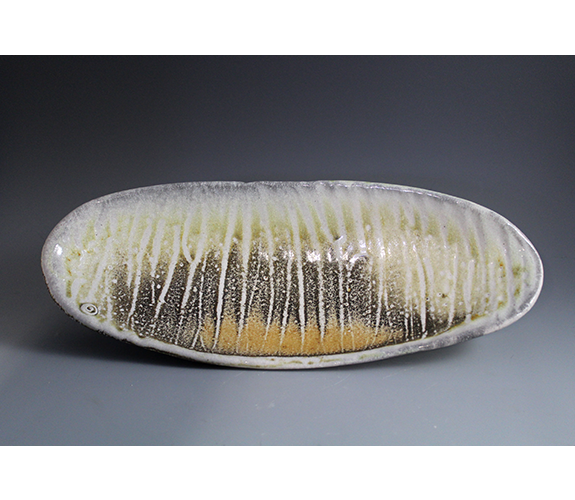
Sodium Vapor firings have been a part of the potter's technology since the 13th century. Developed in Germany using salt as the source of the sodium it was eventually adopted throughout the ceramics industry. Studio potters found the typical "orange peel" texture of the glaze attractive and durable. In most Vapor firings, ware is placed in the kiln unglazed. The potter fires the kiln to the maturing temperature of the clay then introduces a source of sodium into the kiln. The heat of the firing causes the sodium compound to dissociate into sodium ions. The sodium in this form is carried through the ware by the draft of the kiln combining with silica along the way to create a sodium-silicate glaze on everything in the kiln including the ware. Soda firing was developed as a technique for firing ceramics in the 1970's. Developed as an environmentally friendly alternative to the traditional salt firing, soda ash and other sodium compounds were used in place of salt. The results were disappointing though. Unlike salt, other soda compounds do not travel well throughout the kiln and the effects were spotty. It was in the mid-1990s that potters began to see and appreciate the qualities of Soda firing in its own light instead of seeing only soda's inability to reproduce Salt firing glaze effects. Since then, much research has gone into taking full advantage of Soda firing's unique characteristics. Many variables are being tested including basic kiln design, the timing and method of introduction of the soda during the firing, and clay body composition. Other important variables include the form of the work, applied slips and glazes and how and where pieces are loaded into the kiln. Manipulation of the kiln atmosphere (the ratio of air to gas) is also important in the final outcome. With all these variables in play the potential for failure is high. But when everything comes together, Soda firing can produce beautiful and unique results.
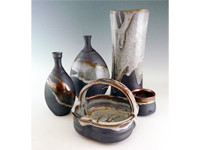
From very early in my life, I have been surrounded by the traditional Japanese arts. My strongest influence was my grandfather’s love of Bonsai, gardens and plants. When I started my ceramic career, this very naturally led to an interest in the art of Ikebana, then to Chanoyu. The study of Tea and the making of the utensils are the key to the aesthetic I am trying to understand. I make tea utensils with the understanding that I have much to learn.
I am more comfortable making flower containers for Ikebana. There is more freedom to explore the potential of a new approach using new materials and glazes. In Ikebana, the container is not viewed as a separate entity, but rather as an integral part of the whole. It must not detract from or overwhelm that which it contains.
Tableware:
For many years, I have come up with numerous reasons to avoid making tableware. The annual series of Glenn Richards Mingei (folk pottery) Pottery Invitational exhibitions has inspired me get over this reluctance and get back to the roots of what we, as functional potters, do. I have gotten surprising pleasure from designing and making items for the table.
Wood firing:
I have joined John Benn and Colleen Gallagher in their venture in wood firing at their kiln on Harstine Island, WA. In all wood fired kilns, happy results are never guaranteed. When the pots do turn out, they are beautiful and unique.